Johnrg
Husqvarna
Pro Class
You are going to replace that fitting with the smaller red anodized one in the kit. The hose is connected to the frame as the top tube works as a catch tank. Any oil there coming from the valve cover vent hose makes it's way back down that tube, so the tube gets cut and routed to the filler plug. It just simplifies things under the engine. That hose was always a PIA to have to remove and replace (just getting a screwdriver on the damn hose clamp) and a potential place to lose your oil. Just bend those holders under the frame and move the hose.
You can see the two hoses here... The one coming up hits the frame behind the wiring and the one buried in the wires goes from the valve cover to a little further up the frame.
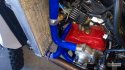
You can see the two hoses here... The one coming up hits the frame behind the wiring and the one buried in the wires goes from the valve cover to a little further up the frame.
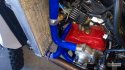