KXcam22
Husqvarna
AA Class
Always lots of head miss-information around. Milling the head on a 2 stroke is an easy way to get more snap in the power band and improve runability, and doesn't increase compression by much. I have done this on almost every 2 stroke I have owned. Contrary to popular opinion, it is not done to increase compression ratio but to improve combustion efficiency by tightening up the squish band. The purpose of the squish band is to force the combustible mixture into the center of the head chamber. The mixture that remains in the squish band gap is cooled by the proximity of the head and piston and does not ignite. Depending on the gap, this “lost” mixture can be as much as 15% of the overall intake charge but usually ranges around 10%. In my case it was 11.3% (calculated) lost charge that did not burn. This represents lost HP. Reduced squish also contributes to improved tolerance to jetting. It is likely that the increased combustion efficiency allows the engine to happily burn less ideal A/F mixtures.
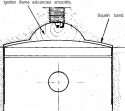
Ideally the squish band should be almost zero, but with the wide variance in tolerances in mass produced motors they can't get there. Why? The piston, rod and cylinder all have production tolerances in length, say +/-0.010" each. If you got a Monday bike the piston could be as much as +0.030" closer to the head than expected. If the factory squish was set at 0.029" then boom. Plus the rod stretches a bit at high RPM so they make the clearance far too big from the factory to be safe. An additional factor is the rod big end bearing clearance. For example, my KX500 had a std 0.010” bearing clearance, meaning the rod could be wiggled up and down about 0.010”. This added an additional 0.005” to the rod stretch value. Not something you would expect and hard to measure. Husky/KTM is also one of the few manufactures that offer different base gasket thickness, which means that once the squish is set that it is importance to always use the same thickness base gasket. Ideally this is set before hand with the proper setup having the piston align with the bottom of the exhaust port at BDC and the top of the cylinder at TDC. My new 300 was closed enough from the factory to not mess with.
If the squish clearance is too large it can sometimes burn and then cause something similar to detonation. It also contributes a bit to pipe bang as the squish mixture goes out the exhaust port and likely contributes somewhat to spooge as well. Most guys with a modified head report a noticeable decrease in pipe bang and spooge. In an ideal world, or if I was still racing, I would set the squish clearance to the bare minimum and then, if required, do some bowl work to increase the volume slightly to keep the compression high but within an acceptable range to run your desired fuel. It takes a lot of compression before top end rev is effected.
An aftermarket head may be better for some, depending on you desire and willingness to mod your bike, but something like 75% of the gain comes from setting the squish band to a more optimum number. The remainder comes from reshaping the bowl or other cool things like the RK Tek head has. In my case I am happy spending $50 to get the 75%. I am suspicious of aftermarket heads or head modifying companies that don’t ask for a squish measurement. It is a necessary requirement to prepare a proper head. The advantage of doing it yourself is that it then becomes a recognized clearance when rebuilding, like setting the X and Z dimensions.
Typical squish clearances are:
50-80cc 0.6-0.8mm
100-125 0.7-0.8mm
175-250 1.0-1.4mm
300-500 1.1-1.5mm
(note: values are per Bell 2 stroke Performance handbook)
These values are from 1973 but I have used them for years and found them to be very good.
Measuring Squish
Squish can be measured in 2 common ways, using a micrometer and the engine dimensions, or by assembling the head with a compressible media on the piston crown and turning the engine over. Common media is modelling clay but resin-core solder it typically used as it is the easiest to measure, and easier for the engine to compress. Solder glued to the piston crown with grease to keep it in place with a small loop in the solder to keep it from rotating. It is important to cut the solder ends with a knife so that the ends are sharp and blunt. Both ends must touch the cylinder wall from L to R. Front to back doesn’t work since the piston will rock on the piston pin and give you odd results. Due to the taper of the squish band it is these ends that give us the measurement, so we want them to be exact and accurate. I use 2 diameters of solder, a before and after, to reduce the amount of stress on the engine. It sucks to buy solder just for measuring squish but I was able to beg some for free from an auto repair shop, since you need less than 6” of each size. The engine must be turned over using the nut on the flywheel and not the kickstarter. When milling the head the final surface must be Oring finish level. A milling machine is best but it can also be done on a lathe with some final lapping of the Oring surface on a piece of glass with 400gr. Not necessary for this application but the ultimate is a final lapping the head to the cylinder with valve grinding paste, but that is messy and only done with the engine apart.
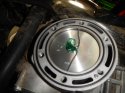
The stock squish clearance on my 2017 300 was 0.0785", measured with 0.110” solder. I milled off a safe 0.028" to leave me a 0.050" squish clearance which is 1.3mm. My actual squish ended up as 1.27mm, measured with 0.060” solder. My compression ratio increased from 13.2 to 13.9, which is not much of an increase. On my 200 EXC the squish is set at .89mm.
I used to do the same head mod with my twin cylinder 2-stroke road racers. On one bike, I had to mill 0.120" off the head and toss the head gasket. That is huge, but the final engine ran nice at 11,500 RPM. In that case the huge squish was an anti-pollution thing as a tight squish speeds up combustion which creates NoX. It might even be a reason why the Euro inspired KTM motors come with such a large squish clearance. More than anyone wanted to know I am sure. Hopefully this info helps somebody. Cam.
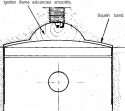
Ideally the squish band should be almost zero, but with the wide variance in tolerances in mass produced motors they can't get there. Why? The piston, rod and cylinder all have production tolerances in length, say +/-0.010" each. If you got a Monday bike the piston could be as much as +0.030" closer to the head than expected. If the factory squish was set at 0.029" then boom. Plus the rod stretches a bit at high RPM so they make the clearance far too big from the factory to be safe. An additional factor is the rod big end bearing clearance. For example, my KX500 had a std 0.010” bearing clearance, meaning the rod could be wiggled up and down about 0.010”. This added an additional 0.005” to the rod stretch value. Not something you would expect and hard to measure. Husky/KTM is also one of the few manufactures that offer different base gasket thickness, which means that once the squish is set that it is importance to always use the same thickness base gasket. Ideally this is set before hand with the proper setup having the piston align with the bottom of the exhaust port at BDC and the top of the cylinder at TDC. My new 300 was closed enough from the factory to not mess with.
If the squish clearance is too large it can sometimes burn and then cause something similar to detonation. It also contributes a bit to pipe bang as the squish mixture goes out the exhaust port and likely contributes somewhat to spooge as well. Most guys with a modified head report a noticeable decrease in pipe bang and spooge. In an ideal world, or if I was still racing, I would set the squish clearance to the bare minimum and then, if required, do some bowl work to increase the volume slightly to keep the compression high but within an acceptable range to run your desired fuel. It takes a lot of compression before top end rev is effected.
An aftermarket head may be better for some, depending on you desire and willingness to mod your bike, but something like 75% of the gain comes from setting the squish band to a more optimum number. The remainder comes from reshaping the bowl or other cool things like the RK Tek head has. In my case I am happy spending $50 to get the 75%. I am suspicious of aftermarket heads or head modifying companies that don’t ask for a squish measurement. It is a necessary requirement to prepare a proper head. The advantage of doing it yourself is that it then becomes a recognized clearance when rebuilding, like setting the X and Z dimensions.
Typical squish clearances are:
50-80cc 0.6-0.8mm
100-125 0.7-0.8mm
175-250 1.0-1.4mm
300-500 1.1-1.5mm
(note: values are per Bell 2 stroke Performance handbook)
These values are from 1973 but I have used them for years and found them to be very good.
Measuring Squish
Squish can be measured in 2 common ways, using a micrometer and the engine dimensions, or by assembling the head with a compressible media on the piston crown and turning the engine over. Common media is modelling clay but resin-core solder it typically used as it is the easiest to measure, and easier for the engine to compress. Solder glued to the piston crown with grease to keep it in place with a small loop in the solder to keep it from rotating. It is important to cut the solder ends with a knife so that the ends are sharp and blunt. Both ends must touch the cylinder wall from L to R. Front to back doesn’t work since the piston will rock on the piston pin and give you odd results. Due to the taper of the squish band it is these ends that give us the measurement, so we want them to be exact and accurate. I use 2 diameters of solder, a before and after, to reduce the amount of stress on the engine. It sucks to buy solder just for measuring squish but I was able to beg some for free from an auto repair shop, since you need less than 6” of each size. The engine must be turned over using the nut on the flywheel and not the kickstarter. When milling the head the final surface must be Oring finish level. A milling machine is best but it can also be done on a lathe with some final lapping of the Oring surface on a piece of glass with 400gr. Not necessary for this application but the ultimate is a final lapping the head to the cylinder with valve grinding paste, but that is messy and only done with the engine apart.
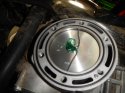
The stock squish clearance on my 2017 300 was 0.0785", measured with 0.110” solder. I milled off a safe 0.028" to leave me a 0.050" squish clearance which is 1.3mm. My actual squish ended up as 1.27mm, measured with 0.060” solder. My compression ratio increased from 13.2 to 13.9, which is not much of an increase. On my 200 EXC the squish is set at .89mm.
I used to do the same head mod with my twin cylinder 2-stroke road racers. On one bike, I had to mill 0.120" off the head and toss the head gasket. That is huge, but the final engine ran nice at 11,500 RPM. In that case the huge squish was an anti-pollution thing as a tight squish speeds up combustion which creates NoX. It might even be a reason why the Euro inspired KTM motors come with such a large squish clearance. More than anyone wanted to know I am sure. Hopefully this info helps somebody. Cam.